BASF Vegetable Seeds, a breeding company that produces high-grade seeds for 24 different vegetable crops, opened its new state-of-the-art breeding facility in the Dutch village of Nunhem in 2018. This has increased the company's capabilities for providing consumers and the supply chain with new vegetable varieties while also applying the latest technology to accelerate the breeding process and reduce its ecological footprint. Now that everything is as good as up and running, it's high time that Priva takes a look at how things are going.
Lead Specialist at BASF René Coumans. "With indoor farming, we can assess crop results as based on facts and can no longer blame the prevailing weather for errors. We're really learning a lot from this."
Massive complex
What you notice right away is BASF's massive complex that occupies a prominent place adjacent to the village of Nunhem in the Dutch province of Limburg. Now standing opposite to the existing complex is a brand-new facility known as GreenEx which consists of about 8.6 acres (3.5 ha) of greenhouses and 183,000 square feet (17,000 m2) of technical facilities used for all breeding activities in cucumber crops. "This addition to our company means having a superb facility for providing our customers with new varietal material that has been developed under optimum conditions. It's also allowing us to respond to three important issues: environmental requirements, safety and plant health," says Peter Keunen, Project Manager at BASF in Nunhem. “With our breeding center, we want set the right path for our plants in order to optimally support their healthy development."
"I've been working here for 20 years now, and as project manager I was closely involved in the design and construction of the new greenhouse complex, which had to respond to important environmental, safety and plant health concerns." Peter Keunen – Project Manager at BASF
Optimizing breeding activities
Indoor farming speeds up the breeding of new varieties
BASF has the latest technology for optimizing its breeding activities. At the existing location, growth chambers with LED lighting (indoor farming) have been built, which eliminates the need for daylight in cultivation. "Our plants grown in these climate-controlled chambers demonstrate the same excellent quality as those from greenhouse cultivation. The great thing about the growth chambers is that we can control absolutely every climate condition as long as we provide these chambers with the right equipment and settings," says René Coumans, Lead Specialist at BASF. “The possibilities for seed crops with regard to breeding programs are endless. With today's knowledge, we can get so much more out of a plant. And indoor farming is a big factor in this. It has involved a substantial investment, of course, but it means we can now assess the development of a crop as based on facts and can no longer blame the prevailing weather for errors. We're really learning a lot from this."
Completely mature cucumber fruits full of seeds
A building management system for seed crops
“The growth chambers are controlled by Priva Blue ID hardware and software for building automation. The knowledge we have about building automation along with our expertise in greenhouse horticulture is proving very useful when it comes to indoor farming. The way we control the climate in buildings can also be applied to controlling the climate of these indoor growth chambers," says Chris Reeskamp, Account Manager at Priva. René Coumans: "The Priva TC Operator software we're using, is working just great. It gives us a uniform system with easy-to-read dashboards that are helping us optimize the parameters for the cultivation process.”
In addition to climate chambers for the cultivation of seed crops, BASF also has cold stores for seed storage. René Coumans: "Seeds remain viable longest in a cold and dry environment.”
Minimizing energy consumption and maximizing water reuse
These greenhouses are real forerunners when it comes to complying with today's environmental standards. Technologies for energy conservation and the use of diffused glass create a uniform climate and reduce natural gas consumption by up to 48 percent. "Energy is one of the largest costs for horticultural businesses," says Rene Hofman, Project Leader at Priva. "The control modules in our Priva Connext process computer integrate multiple systems and are able to calculate variable conditions in advance and then anticipate them automatically. This means substantial savings on energy, water and CO2."
Water control systems play an important role in the new breeding center. The repeated recycling, disinfecting and purification of the cultivation water practically eliminates wastewater. "We've designed our technical water management system with the future in mind and are currently producing practically no emissions," says Albert Vermaak, Water Specialist at the Nunhem location. Contributing to this is the Priva Vialux E-Line purification system for effluent water. "Since May 2019, we have been certified by the BZG (Assessment Committee for Greenhouse Horticulture Purification Installations) which means that our effluent water is free of at least 95 percent of crop protection products. Actually, at 99.5 percent we exceed the Dutch legal requirement. Our goal for 2027 is to reach a zero-discharge water cycle that allows us to recirculate all of our cultivation water.
From left to right: Chris Reeskamp (Account Manager, Priva), Robert Bovend’Eerdt (Technical Coordinator, BASF), Albert Vermaak (Water Specialist, BASF)
Smart data connection for optimizing crop results
Data-based horticulture is becoming increasingly important. The real-time monitoring of a crop can optimize crop strategy. BASF therefore chose to use 30 MHz wireless climate sensors that are connected to a Priva process computer. This provides insight into cultivation processes and gives the company a platform that visualizes all the cultivation data in easy-to-read dashboards. This way, the various measurements are easily monitored and made accessible to provide a clear picture of the climate throughout the greenhouse.
Making this data available also gives the company another advantage: "One of our challenges is safeguarding knowledge and passing it on to new employees," says Rob Wouters, Cultivation Specialist at BASF. "Even new employees with a professional background in horticulture will often require years of internal training. The 30 MHz connection also means we can explain our cultivation processes better to new colleagues."
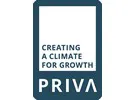
Priva
Zijlweg 3
2678 LC De Lier
Netherlands
T: +31 88 200 5000
contact.priva@priva.nl
www.priva.com