The trays consist of two layers- the top layer holds the medium and the seedlings. It is designed as an alternative to Styrofoam; Because of its hard material the roots of the seedlings cannot infiltrate to the tray. This saves the plants from damage while replanted. The bottom layer is rigid, provides support, reusable after rinsing, can be suspended on propagation rails and can even float on water. The latter is a very important feature, as the most productive and commonly used method for tobacco seedlings is the floating, hydroponic system. Currently growers mainly use Styrofoam, but these trays result in a bigger carbon dioxide footprint, are lower in hygiene standards, they are more expensive and the roots of the plants can get injured while they are replanted.
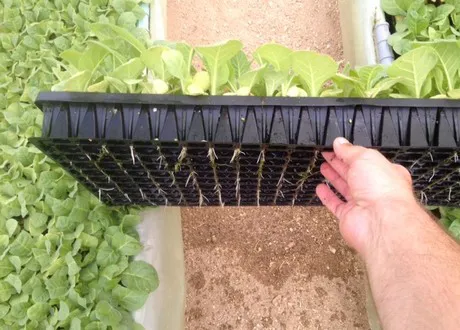
Jacob Tsonakis from INA Plastics spoke about the system. “The tobacco industry is regulated very strictly, and also the production is subject to heavy rules. The TOBACCO-TRAY is a great opportunity for growers to easily change to something better, eco-friendly and more economical. The bottom layer can carry up to 12 kg of weight, it is reusable and ensures magnificent growing characteristics. As it lets water in and keeps the growing medium wet, it provides all the advantages of similar Styrofoam products.”
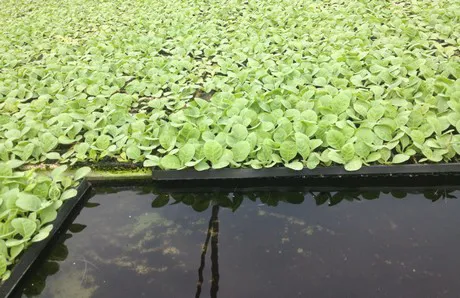
Lately the company has started designing a similar system for hydroponic vegetables, especially lettuce production. As Mr Tsonakis said, “Consumers are more and more interested in buying more and healthier vegetables, which is a great opportunity for hydroponic vegetable production. We saw that our Double Tray System (DTS) is particularly popular among tobacco growers and we realised that it could offer many advantages in vegetable production as well. Thus, we have started designing a similar system for them, which we will introduce in a couple of weeks.”
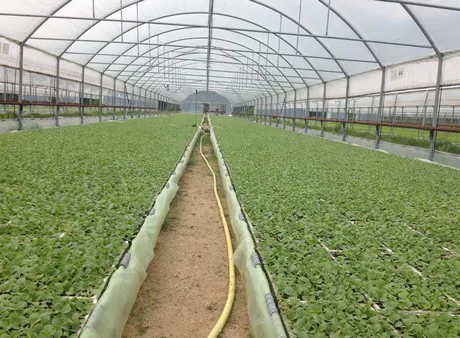


As he explained, these trays would have a greater added value, the “one-fits-all” principle. “We would like to enable growers to use one system throughout the production cycle. For example in cases of lettuce, the growers could sow the seeds into a 54-cell raft. After a while, when the plants are growing, they could be replanted basically to the same tray just with bigger spaces. At the end of the production there would be six full-grown lettuces on the tray.”-he said.
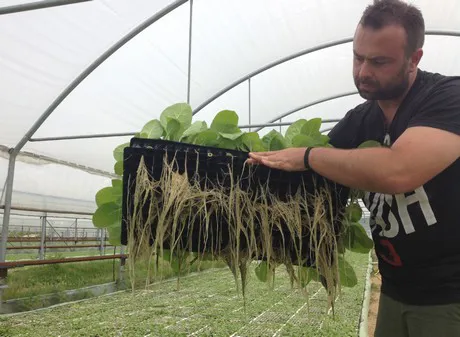
As Mr Tsonakis concluded “Our Systems offer great opportunities and excellent growing characteristics for every grower, who is aiming to make the production cheaper, more practical and more environmentally friendly. And who wouldn’t want that?”
By Luca Utassy and Boy de Nijs
For more information
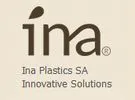
Jacob Tsonakis
117, Megaridos street
19300 Aspropyrgos
P.O. Box 64
Tel: +30 210 5580126
Fax: +30 210 5574731
[email protected]
[email protected]
www.ina-plastics.com